PPWD specialises in the design and delivery of diverse human factors training. From non-technical skills, communications and trauma workshops through investigations and learning reviews to fair culture, well-being and leadership programmes. Our expert facilitators create learning from the boardroom to the frontline that sticks long after the classroom. PPWD’s Compassionate Safety approach generates safe environments that accommodate humans for being human. Our approach aligns personal and organisational mindsets, beliefs and values. In doing so, workplaces are created where people thrive and flourish; here colleagues demonstrate their best self. Through the development of self-awareness and awareness of others, the physical, psychological and emotional factors become equal safety priorities and result in colleagues who possess a clarity of vison, are calm, understanding and agile in action. Colleagues who are sensitive to the hazards and risks of their environment, and confident to be safety leaders for themselves, others and the organisation.
Project Testimonials
‘At Southeastern, our journey towards embedding a fair culture has been supported by PPWD at every step. From early conception to the launch of our Fair Culture Charter we have worked collaboratively with Paul Davison. Whilst acting as consultants, PPWD have immersed themselves into our organisation and are effectively seen as an extension to our team of safety professionals and have helped to guide us in the right direction, checking in along the way and supporting the development of our culture change programme. Steve Lewis – Head of Safety and Environment – SE
‘We’ve replaced the old finger-pointing culture of blame with something much more positive, much more inclusive, and much more useful. Hence, we’ve not only moved away from accidents and incidents to learning events, but we’ve also moved away from ‘investigations’ to ‘learning reviews’ too.’ – Jon Cole – Operations Standards Specialist – SE
‘There’s little value in fixing the human if another similarly trained and experienced human can make the same (or similar) error. With this in mind, I always ask ‘could I have made the same mistake myself?’ If the answer is yes, then we try to work out how the business, how the system, could have created a situation where that kind of mistake was possible.’ – Jon Cole – Operations Standards Specialist – SE
‘To be listed as finalists is a wonderful acknowledgement of the investment of energy, persistence and a commitment by both the Southeastern and PPWD teams. All of the results gained through this project have been hard won. Alone, those results are wonderful feedback. The change in culture and the impact on colleagues has been immense. However, to gain external recognition, a validation that what has been achieved has value and is significant. This has spurred us on to partner with other organisations to evolve fairer culture for them as well.’ – Paul Davison – CEO and Founder – PPWD
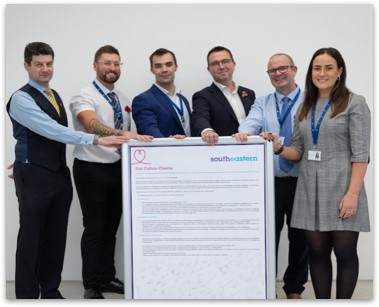
Southeastern Project
Why didn’t I know this 20 years ago?”. This is a powerful quote from a train drivers’ union rep on a pilot course in 2015. The success of these pilot courses led to PPWD being selected to deliver non-technical skills (NTS) courses to drivers, which was part of a wider incident reduction project.
The NTS courses were highly facilitated sessions framed around the Rail Safety and Standards Board’s (RSSB) seven categories and 26 skills, such as Situation Awareness and Communication. They centred on the information processing model – the ‘rules of the mind’. The idea behind this is that if those in safety-critical roles understand the limitations of their senses, memory and processing abilities, they will make more effective decisions, hopefully resulting in safer actions.
Overlay this understanding with wellbeing, mindfulness, and a better understanding of the impacts of pressure, stress, sleep and fatigue, and you arm safety-critical staff to more effectively manage daily stressors. An individual with improved wellbeing is more likely to employ effective NTS, which leads to more effective role-specific technical skills and safer actions.
By employing adult learning methods such as dialogue, case studies, shared experiences and practical exercises, delegates were able to explore human performance topics from a range of perspectives. This resulted in learning which has stuck long after the classroom.
The anecdotal, critical and statistical feedback generated senior management interest and a cultural evolution began. What had been the preserve of train services migrated to all business areas. Passenger, engineering, commercial and HR wanted to be part of the evolution. As these conversations developed, it became possible to weave a cultural tapestry including psychological safety, inclusivity, equality and diversity. All SE employees had a role in being safety leaders and generating a fair culture.
The next step was the change from investigations to Learning Reviews (LR). There was a shift towards prevention of recurrence – factors such as work-as-done and ‘what had gone wrong’ replaced rule breaches, causes and ‘who had gone wrong’. This freed participants to offer the truth and to be part of the solution. Almost immediately, pre-accident, system stress-testing and group learning reviews became ‘just what we do around here’. The LRs informed business plans, resource allocation and an investment in safety capacity.
A Fair Culture Charter was launched last year, applicable to all SE employees as a set of binding principles. At a recent meeting, a presentation was delivered on a new policy. At the end, the MD and a director asked the presenter how it fitted with the Fair Culture Charter. Unable to answer, the individual was asked to redraft the policy.
Monthly Operational Learning Reviews (OLR) were key to the success of the project and gave people a chance to work together on issues. One example of where this could be seen to deliver benefits was in the approach to Signals Passed at Danger (SPAD) – a sensitive topic in the rail industry. Even with a suite of automatic protection systems, there is a very real risk that any SPAD could result in fatalities. Occasionally, there’s a cluster of SPADs, which nearly always triggers a knee-jerk response. Instead, the OLR and Head of Drivers worked together to maintain a steady state, responding to adverse events by looking at ‘what went wrong’, rather than ‘who went wrong’. They could then look at the long-term strategy and see how the adverse event modified what was already in place.
Results
– 64% reduction in operational adverse events.
– ROI of 1.4 in Year 1 and then 4.7 in year 2.
– Reduction in staff turnover, disciplinaries and absenteeism.
– Increase in dialogue between frontline and management focused on the co-creation of safety.
– Increase in reporting and identification of eroded safety margins before the adverse event occurs.
– Net Promoter Score – 93+ out of 100.
– Course Critique Average – 9.5/10.
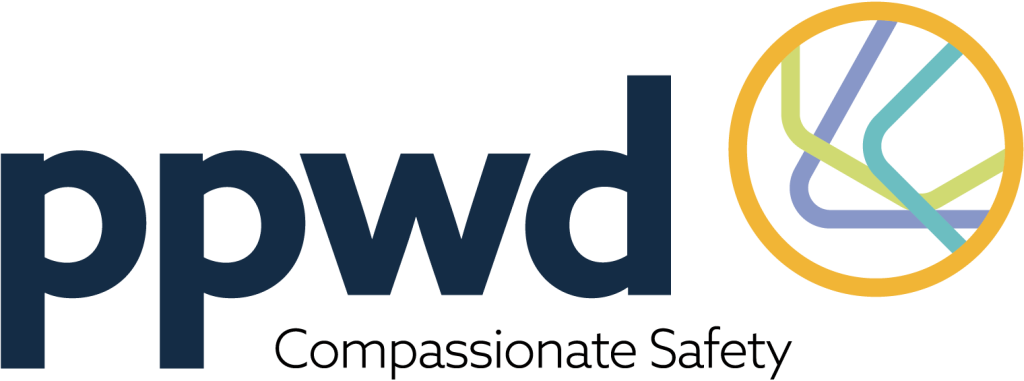